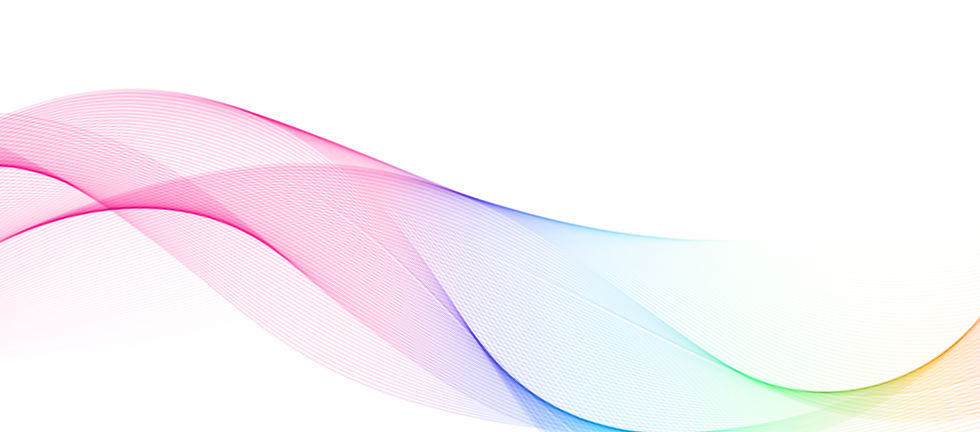
Problems & Solutions
Adhesion Problem After Curing
Powder coating may not be sufficiently baked, check.
The paint thickness may be too large, reduce the paint spraying capacity.
The surface to be painted may not be clean enough, check the cleaning agents and tools.
Contact the paint manufacturer.
Non-Standard Color Formation at the End of Painting
Check the paint thickness, increase it if the thickness is thin.
Make sure the paint thickness is homogeneous.
Check the air circulation conditions in the furnace flue and furnace.
Check the paint used in another oven, if the paint comes out as desired, it means that there is an error in the other oven.
Coverage of the paint may not be sufficient, contact the paint manufacturer.
Orange Look
Check the paint thickness and make sure it is 60-70 microns.
Oven heating speed may be slow, check oven.
The voltage may be high, optimize.
The paint may be too reactive or too coarse, contact the paint manufacturer.
Perforation and Outgassing in Painted Film
Check the paint thickness, if the paint thickness is over 100 microns, reduce the paint thickness.
The surface to be painted may be wet, check the dryer and filters.
If you don't have an air dryer, have it installed.
It can be caused by moisture in the paint. Check the storage conditions and the humidity in the air carrying the paint.
If the material is porous, such as a cast, galvanized surface, preheat the material.
Contact the paint manufacturer and ask for a powder coating that is special for gaseous surfaces.
Low Resistance to Chemical Substances
It may be caused by insufficient baking, check the curing temperature and time.
If resistance to solvents is the user's request, contact the powder coating manufacturer and request a paint that is resistant to these solvents.
Low Resistance to Corrosion
Surface treatment may be insufficient, check surface treatment and equipment.
It may be caused by insufficient baking, check the curing temperature and time.
Contact the powder coating manufacturer for advice on improving corrosion resistance.
Insufficient Surface Hardness
-
Check whether the baking is sufficient, if the oven is not adjusted, bring it to the desired position, increase the temperature and time as the material thickness increases. If the problem cannot be resolved, contact the company.
Crater Formation
All kinds of foreign matter that changes the surface tension can create a crater on the surface to be painted (silicone, welding gas, heavy perfume, oil, mixing with different paints, etc.), remove the foreign matter in the environment.
Prevent external factors by creating positive pressure in the painting booth.
Crater may occur due to incompatibility with other paint, clean the paint booth in detail.
It may be caused by paint, contact the manufacturer.
Formation of Different Thicknesses on the Painted Film
If the shape of the part being painted is too indented, change the gun and hanger position.
Check the distance of the gun from the painted part.
Adjust air charge if gun air builds up paint in some areas.
Check the grounding, make sure the hangers are clean.
It may be due to the fine particle size of the powder coating.
Check the recycle dye ratio, reduce if excessive.
Low Impact Resistance
Check whether the baking is sufficient, if the oven is not adjusted, bring it to the desired position, increase the temperature and time as the material thickness increases.
Check the paint thickness, reduce it if it is too thick.
Check that the surface cleaning and pre-treatment are done correctly.
It may be caused by paint, contact the manufacturer.
Insufficient Powder Flow
The air carrying the powder coating may be insufficient. Try again by increasing the air pressure.
If there is dust in the powder coating boiling chamber, reduce the powder boiling air pressure.
Hoses may be squashed, kinked or pinched. Check the hoses for this.
The powder coating may be too thin, check the return dye addition rate, add fresh dye if necessary.
Paint may be damp, check storage conditions and store at room temperature.
Poor Adhesion of Powder to Material
Check the grounding.
The voltage may be high, check.
If there is no voltage, the paint cannot be charged, check.
Paint may be too fine-grained, check return addition rate, add fresh paint if necessary.
Check the surface treatment, the surface treatment may not be able to wet the welded surface.
Check the distance between gun and material.
Frame Effect
Powder coating grains may be coarse, contact the manufacturer.
The voltage may be too high, check.
Distance between gun and material may be too low, check.
The air velocity carrying the paint may be high, check it.
Back Ionization
The voltage may be high, reduce it.
Gun may be too close to material, check.
Powder coating grains may be too fine, check return rate, add fresh dye if necessary.
Fresh paint may be fine grained, contact paint manufacturer.
Clumping in the Box
Storage conditions may not be suitable, check, ventilate and sift before use.
The fluidity or storage stability of the powder coating may be low, contact the paint manufacturer.
Puffing During Pulse
Pressure settings may vary, check.
The carrier air may be humid, check.
Powder coating grains may be very fine, if using return, check the addition ratio and add fresh dye.
Nozzles may be worn, replace them.
Powder coating can be damp, pay attention to the temperature difference between the storage condition and the area it is painted.
Unpainted Region Formation at Indented Edges
May be caused by gun airflow. If the airflow is high, decrease it, if it is low, increase it.
Paint may be caused by the deflector diameter, if the deflector diameter is large, use a small diameter deflector.
The voltage value may be too high, lower the voltage a little.
Check for kinks and solder on unpainted areas.
Do the cleaning of these areas well, if not done well, there may be evaporation in the oven.
Also, adjust the gun position towards these areas.
If there is an unpainted area, check with a hand gun.
Powder coating can be very thin. Continue painting by reducing the return dye ratio.